Технологический процесс ручной дуговой сварки. Подготовка кромок под сварку
Самое элементарное, что нужно знать начинающему сварщику, это то, как соприкасаются между собой сварные детали. В зависимости от проектного положения, по правилам ГОСТ и СНиП существуют разные виды сварных соединений, как показано на рисунке ниже. Это касается не только пластин, но и уголков, швеллеров, труб, квадратов и других прокатных изделий.
Ни одно более-менее серьезное строительное производство не обходится без применения низкой и средней мощности. В меньшем количестве случаев (когда нет доступа к электричеству) виды сварных швов выполняются , которая менее распространена по причине ее большей громоздкости.
В любом случае, мало знать и уметь пользоваться сварочным аппаратом для того, чтобы сварить те или иные детали. Важно знать, какие бывают виды сварного шва, то есть, как производить обработку кромок деталей для их состыковки, фиксации в том или ином пространственном положении и дальнейшей их сварки.
Как правило, тот или иной вид шва сварного соединения формируется при помощи электроинструмента – болгарка с двумя типами кругов: отрезной по металлу и угловой шлифовальный. Первый предназначен для обрезки детали под тем или иным углом, второй – для обработки, их отрезных поверхностей, шлифованию, чтобы они ровно прилегали друг к другу. Кроме того, сам сварочный аппарат способен работать в режиме резки.
В данном случае обе детали соединяются торцами, которые заранее специальным образом обрабатывают, либо оставляют необработанными. Это зависит от толщины металла деталей, стыковое соединение которых предполагается выполнить.
Также стоит обратить внимание (рис) на то, что может быть обработан торец только одной детали, что позволяет уменьшить расход металла, сварочной проволоки при солидной толщине деталей. Кроме этого, виды стыковых соединений могут быть обработаны с одной стороны – для односторонней сварки и с двух сторон – для двусторонней сварки.
Соединение без разделки не обрабатывается каким-либо образом, только возможно убираются зазубрины, неровности и шероховатости, чтобы совершить состыковку с зазором не более 2 мм, как положено по ГОСТ. Бывает односторонним и двухсторонним, соответственно рассчитано на сварные стыковые соединения деталей, толщина металла которых не превышает 4 мм и 8 мм соответственно.
Соединение со скосом торцов выполняется во многих вариациях, как показано на рис. Это может быть и односторонний ровный/овальный скос кромки, и двусторонняя разделка, так называемый V-образный, U-образный скос. Применяются все эти типы стыковых соединений для деталей с толщиной металла 4-25 мм с зазором 1-2 мм.
Соединение с двусторонней разделкой имеет смысл выполнять при толщине свариваемой детали от 12 мм, так как именно с этой величины начиная можно заметить снижение расхода материала для сварки, металла. При этом и сама сварка стыковых соединений происходит быстрее, чем в случае с односторонней разделкой кромок по V-образному или U-образному способу, а расход сварочных материалов уменьшается в два раза как минимум.
Как можно заметить, детали имеют положение, напоминающее букву «Т», отсюда именуется как тавровое соединение, при котором одна деталь находится перпендикулярно относительно второй. Таким образом, сваркой соединяется поверхность кромки одной детали с плоскостной поверхностью второй. Соответственно, обрабатываться разделкой может лишь одна деталь, как на рисунке ниже.
Соединение без разделки сваривается с двух сторон и применяется для деталей одинаковой толщины металла, не превышающей 10 мм. Никакой особой обработки кромки перпендикулярно расположенной детали не применяется, лишь шлифование при необходимости для плотного прилегания кромки к плоскости (до 2 мм зазор). Важно учесть, что сварка тавровых соединений без разделки отличается в случае, если перпендикулярно расположенная (вертикально стоящая) деталь имеет меньшую толщину, чем вторая, горизонтально примыкающая. Просто электрод ставят под углом 60 градусов к более толстой детали, что способствует большему ее плавлению.
Соединение с разделкой выполняется в случае, если требуется особо прочный шов и тавровое сварное соединение имеет перпендикулярно размещающуюся (вертикально стоящую) деталь, толщина металла которой больше, чем 10 мм (как минимум – 8 мм). Это может быть и одностороння и двусторонняя разделка, при этом кромку обрезают прямолинейно, под углом 45 градусов. Так, сварка большой толщины деталей происходит в несколько слоев, пока не заполнится все около разделочное пространство.
В случае, когда производится соединение внахлест, одна деталь располагается на другой, сварка происходит по кромкам обеих деталей. При этом разделки кромок не предусматривается технологически, лишь подготовка для плотного прилегания одной плоскости ко второй. Соединяются детали двумя сварными швами, которые связывают кромки с ближе лежащими плоскостными поверхностями.
Соединение без усиления целесообразнее всего производить при соединение внахлестку деталей, имеющих толщину не более 10 мм. Двойной шов в этом случае выполняют из соображений по герметизации, то есть для того чтобы влага не попадала между нахлестом и не происходил усиленный процесс коррозии. Сам способ соединения называется «соединение внахлестку с лобовыми швами».
Соединение с усилением выполняется при особых требованиях к прочности, а также при большой толщине металла свариваемых изделий. На рисунке показано сварное соединение внахлест с дополнительными сварными креплениями, которые получают путем прогревания нижней и проплавления верхней детали, а также те, которые заранее пропиливают в месте сварного соединения. Кроме вспомогательных креплений, в редких случаях они могут также выполняться без лобовых швов при небольшой толщине изделий, но в таком случае на особую прочность не стоит рассчитывать.
Данное соединение отчасти похоже на тавровое из-за перпендикулярно размещенных сварных деталей. Подобно тавровому, угловое соединение обрабатывается лишь одной стороной кромки, вторая также участвует в сварном процессе, но разделке не подвергается, лишь ровной обрезке строго под 90 градусов и шлифовке от заусениц, зазубрин и т. д., остальных деффектов.
Соединение без разделки кромки, как показано на рис, производится со смещением детали из-под заподлицо второй кромки. При этом сварочный шов соединяет оба торца с наружной стороны, но угловые сварные соединения могут также быть дополнительно усилены и вторым швом, выполненным с внутренней стороны угла. При этом второй шов сваривает внутренние плоскости деталей, при этом увеличивается расход материала для сварки и время сварки, но получается крепчайшее сварное соединение.
Соединения с разделкой кромки применяются в случае большой толщины деталей, как и при тавровых соединениях. Односторонняя или двусторонняя разделка кромки нужна в случае, если выполняется сварка угловых соединений деталей с толщиной от 8 мм до 25 мм. При односторонней разделке выходит очень глубокий шов, в связи с этим сварку производят в 2-3-4 слоя. Двусторонняя V-образная сварка куда более экономичная и быстрая в производстве во многих случаях.
Это была статья про подготовку и состыковку сварных соединений под ручную сварку – малейшая крупинка в познании процессов сварочного производства. Отдельной темой является то, как виды сварных соединений и швов, описанных ранее, произвести тем или иным типом сварки.
Оглавление книги Следующая страница>>
Подготовка кромок под сварку. Форма подготовленных кромок под сварку .
Подготовка кромок под сварку. К элементам геометрической формы подготовки кромок под сварку (рис. 25) относятся угол разделки кромок α, притупление кромок S, длина скоса листа L при наличии разности толщин металла, смещение кромок относительно друг друга б, зазор между стыкуемыми кромками а.
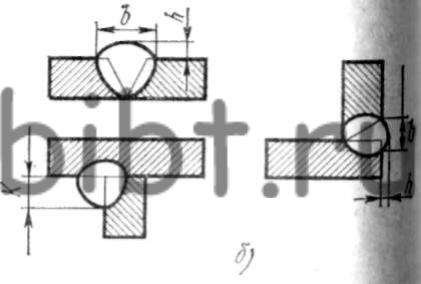
Рис. 25. Элементы геометрической формы подготовки кромок под сварку (а) и шва (б):
в - ширина шва, h - высота шва, К - катет шва
Угол разделки кромок выполняется при толщине металла более 3 мм, поскольку ее отсутствие (разделки кромок) может привести к непровару по сечению сварного соединения, а также к перегреву и пережогу металла; при отсутствии разделки кромок для обеспечения провара электросварщик должен увеличивать величину сварочного тока.
Разделка кромок позволяет вести сварку отдельными слоями небольшого сечения, что улучшает структуру сварного соединения и уменьшает возникновение сварочных напряжений и деформаций.
Зазор, правильно установленный перед сваркой, позволяет обеспечить полный провар по сечению соединения при наложении первого (корневого) слоя шва, если подобран соответствующий режим сварки.
Длиной скоса листа регулируется плавный переход от толстой свариваемой детали к более тонкой, устраняются концентраторы напряжений в сварных конструкциях.
Притупление кромок выполняется для обеспечения устойчивого ведения процесса сварки при выполнении корневого слоя шва. Отсутствие притупления способствует образованию прожогов при сварке.
Смещение кромок создает дополнительные сварочные деформации и напряжения, тем самым ухудшая прочностные свойства сварного соединения. Смещение кромок регламентируется либо ГОСТами, либо техническими условиями. Кроме того, смещение кромок не позволяет получать монолитного сварного шва по сечению свариваемых кромок.
ГОСТ 5264-80 предусматривает для стыковых соединений формы подготовленных кромок, представленные на рис. 26; для угловых соединений - на рис. 27; тавровых - на рис. 28 и нахлесточных - на рис. 29.
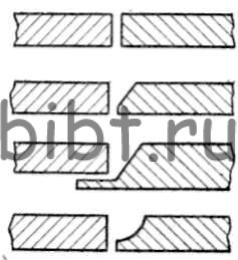
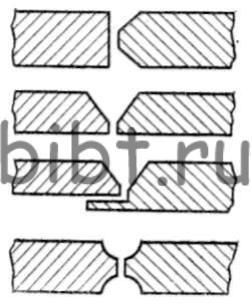
Рис. 26. Форма подготовленных кромок под сварку для стыковых соединений
Рис. 27. Форма подготовленных кромок под сварку для угловых соединений

Рис. 28. Форма подготовленных кромок под сварку для тавровых соединений
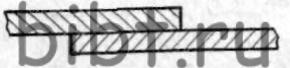
Рис. 29. Форма подготовленных кромок под сварку для нахлесточных соединений
Подготовку кромок под сварку выполняют на механических станках -токарных (обработка торцов труб), фрезерных, строгальных - обработка листов и т. д., а также применением термической резки. Листы, трубы, изготовленные из углеродистых сталей, обрабатываются газокислородной резкой. В качестве горючих газов могут служить ацетилен, пропан, коксовый газ и т. д. Цветные металлы, а также нержавеющие стали обрабатываются плазменной резкой.
Перед сваркой особо ответственных конструкций торцы труб или листов после газокислородной резки обрабатывают дополнительно механическим путем; это делается для того, чтобы избежать каких-либо включений в металле.
РАЗДЕЛКА КРОМОК ПОД СВАРКУ
Разделка кромок - придание кромкам, подлежащим сварке, необходимой формы.
Разделка кромок под сварку выполняется с целью обеспечения:
Провара по всей толщине свариваемых элементов;
Доступа сварочного инструмента к корню шва.
По форме разделки кромок под сварку различают сварные соединения без разделки кромок, с отбортовкой и с разделкой кромок под сварку. Кроме того, сварные соединения с разделкой кромок подразделяются на сварные соединения с односторонним скосом одной или двух кромок (односторонняя разделка одной или двух кромок) и сварные соединения с двусторонним скосом одной или двух кромок (двусторонняя разделка одной или двух кромок).
При выборе формы разделки кромки следует учитывать, что наиболее экономичным является сварное соединение без скоса кромок. В случае выполнения разделки кромок более простой в исполнении по сравнению с U – образной является разделка кромок с прямолинейным скосом кромок (V, К, Х – образные). В сравнении с односторонней разделкой кромок более технологичными являются К- и Х-образные двусторонние. Однако К- и Х-образные двусторонние могут быть реализованы при возможности доступа сварочного инструмента к обеим сторонам изделия.
Конструктивные элементы формы разделки кромок.
Конструктивные элементы формы разделки кромок зависят от конструктивных особенностей свариваемых элементов, а также от диаметра электродного материала (размеры разделки кромок должны обеспечивать доступ электрода или сварочной проволоки к корню шва).
Форма разделки кромок характеризуются следующими основными конструктивными элементами: зазор b, притупление С, угол скоса кромки β и угол разделки кромок α.
Угол скоса кромки β.
Скос кромки - прямолинейный срез кромки, подлежащей сварке.
Угол скоса кромки - острый угол между плоскостью скоса кромки и плоскостью торца.
Угол скоса кромки β изменяется в пределах от 30 ± 5 до 10 ± 5 градусов. При разделке одной кромки угол скоса кромки может составлять 45 градусов.
Угол разделки кромок - угол между скошенными кромками свариваемых частей. Угол разделки кромок α= 2 β. Угол разделки кромок выполняется для обеспечения доступа электрода к основанию шва.
Притупление кромки - нескошенная часть торца кромки, подлежащей сварке. Назначение притупления - обеспечить правильное формирование сварного шва и предотвратить прожоги в корне шва. Притупление кромок С обычно составляет 2 мм ± 1 мм. Иногда, в связи с конструктивными особенностями сварного соединения, значение притупления может приниматься равным нулю (С=0). В этом случае необходимо предусматривать технологические мероприятия, исключающие появление прожога (сварка на подкладке, сварка на флюсовой подушке, укладка подварочного шва, применение замкового соединения).
Зазор - кратчайшее расстояние между кромками собранных для сварки деталей. Зазор b обычно равен 1,0 - 3 мм, так как при принятых углах разделки кромок наличие зазора необходимо для провара корня шва, но в отдельных случаях, при той или иной технологии, зазор может быть равным нулю или достигать 8-10 мм и более. Если зазор b = 0, выполняемая сварка называется сваркой без зазора, если b ≠ 0 –сваркой с зазором (или по зазору).
БЕЗ РАЗДЕЛКИ КРОМОК |
§ 28. Подготовка металла под сварку
Подготовка поверхности металла под сварку. При подготовке деталей под сварку поступающий металл подвергается правке, разметке, наметке, резке, подготовке кромок под сварку, холодной или горячей гибке.
Металл правят либо вручную, либо на различных листоправильных вальцах. Ручную правку выполняют на чугунных или стальных правильных плитах ударами кувалды или с помощью ручного винтового пресса. Угловая сталь правится на правильных вальцах (прессах), двутавры и швеллеры - на приводных или ручных правильных прессах.
Разметка и наметка - это такие операции, которые определяют конфигурацию будущей детали. Механическая резка применяется для прямолинейного реза листов, а иногда для криволинейного реза листов с использованием для этой цели роликовых ножниц с дисковыми ножами. Углеродистые стали разрезают газокислородной и плазменно-дуговой резкой. Эти способы могут быть ручными и механизированными. Для резки легированных сталей, цветных металлов может применяться газофлюсовая или плазменно-дуговая резка.
Основной металл и присадочный материал перед сваркой должны быть тщательно очищены от ржавчины, масла, влаги, окалины и различного рода неметаллических загрязнений. Наличие указанных загрязнений приводит к образованию в сварных швах пор, трещин, шлаковых включений, что приводит к снижению прочности и плотности сварного соединения.
Подготовка кромок под сварку. К элементам геометрической формы подготовки кромок под сварку (рис. 25) относятся угол разделки кромок α, притупление кромок S, длина скоса листа L при наличии разности толщин металла, смещение кромок относительно друг друга б, зазор между стыкуемыми кромками а.
Рис. 25. Элементы геометрической формы подготовки кромок под сварку (а) и шва (б):
в - ширина шва, h - высота шва, К - катет шва
Угол разделки кромок выполняется при толщине металла более 3 мм, поскольку се отсутствие (разделки кромок) может привести к непровару по сечению сварного соединения, а также к перегреву и пережогу металла; при отсутствии разделки кромок для обеспечения провара электросварщик должен увеличивать величину сварочного тока.
Разделка кромок позволяет вести сварку отдельными слоями небольшого сечения, что улучшает структуру сварного соединения и уменьшает возникновение сварочных напряжений и деформаций.
Зазор, правильно установленный перед сваркой, позволяет обеспечить полный провар по сечению соединения при наложении первого (корневого) слоя шва, если подобран соответствующий режим сварки.
Длиной скоса листа регулируется плавный переход от толстой свариваемой детали к более тонкой, устраняются концентраторы напряжений в сварных конструкциях.
Притупление кромок выполняется для обеспечения устойчивого ведения процесса сварки при выполнении корневого слоя шва. Отсутствие притупления способствует образованию прожогов при сварке.
Смещение кромок создает дополнительные сварочные деформации и напряжения, тем самым ухудшая прочностные свойства сварного соединения. Смещение кромок регламентируется либо ГОСТами, либо техническими условиями. Кроме того, смещение кромок не позволяет получать монолитного сварного шва по сечению свариваемых кромок.
ГОСТ 5264-80 предусматривает для стыковых соединений формы подготовленных кромок, представленные на рис. 26; для угловых соединений - на рис. 27; тавровых – на рис. 28 и нахлесточных - на рис. 29.
Рис. 26. Форма подготовленных кромок под сварку для стыковых соединений
Рис. 27. Форма подготовленных кромок под сварку для угловых соединений
Рис. 28. Форма подготовленных кромок под сварку для тавровых соединений
Рис. 29. Форма подготовленных кромок под сварку для нахлесточных соединений
Подготовку кромок под сварку выполняют на механических станках - токарных (обработка торцов труб), фрезерных, строгальных - обработка листов и т. д., а также применением термической резки. Листы, трубы, изготовленные из углеродистых сталей, обрабатываются газокислородной резкой. В качестве горючих газов могут служить ацетилен, пропан, коксовый газ и т. д. Цветные металлы, а также нержавеющие стали обрабатываются плазменной резкой.
Перед сваркой особо ответственных конструкций торцы труб или листов после газокислородной резки обрабатывают дополнительно механическим путем; это делается для того, чтобы избежать каких-либо включений в металле.
Требования к сборке металлических деталей перед сваркой. Применяемые сборочно-сварочные приспособления должны обеспечивать доступность к местам установки деталей и прихваток, к рукояткам фиксирующих и зажимных устройств, а также к местам сварки. Эти приспособления должны быть также достаточно прочными и жесткими, обеспечивать точное закрепление деталей в нужном положении и препятствовать их деформированию в процессе сварки. Кроме того, сборочно-сварочные приспособления должны обеспечивать наивыгоднейший порядок сборки и сварки: наименьшее число поворотов при наложении прихваток и сварных швов; свободный доступ для проверки размеров изделий и их легкий съем после изготовления; безопасность сборочно-сварочных работ.
Любая сборочная операция не должна затруднять выполнение следующей операции. Поступающие на сборку детали должны быть тщательно проверены; проверке подлежат все геометрические размеры детали и подготовленная форма кромок под сварку.
Сборка сварных конструкций, как правило, осуществляется либо по разметке, либо с помощью шаблонов, упоров, фиксаторов или специальных приспособлений - кондукторов, облегчающих сборочные операции. Подготовку и сборку изделий под сварку выполняют с соблюдением следующих основных обязательных правил:
притупление кромок и зазоры между ними должны быть равномерными по всей длине;
кромки элементов, подлежащих сварке, и прилегающие к ним места шириной 25-30 мм от торца кромки должны быть высушены, очищены от грата после резки, масла, ржавчины и прочих загрязнений;
во избежание деформаций прихватку следует выполнять качественными электродами через интервал не более 500 мм при длине одной прихватки 50-80 мм;
для обеспечения нормального и качественного формирования шва нужно в начале и в конце изделия прихватывать планки.
В подготовку металла под сварку входит правка, разметка и наметка, резка и обработка кромок, холодная и горячая гибка. Правка производится преимущественно на станках, а иногда вручную. Листовой, полосовой и профильный прокат правят на вальцах, которые чаще всего имеют семь или девять валков.
Вальцы оборудуются двумя роликовыми столами для загрузки и выхода металла в процессе правки. При правке листы пропускают через вальцы от 3 до 5 раз.
Наряду с машинной правкой иногда применяют ручную правку. Последнюю производят на чугунных или стальных правильных плитах ударами молота, кувалды и при помощи винтового пресса.
Правку угловой стали производят на углоправильных вальцах или на ручных винтовых прессах, а двутавров и швеллеров -- на приводных или ручных правильных прессах.
Разметка и наметка. При индивидуальном производстве выправленный металл поступает на разметку, а при массовом и серийном производстве поступает для наметки. Перед разметкой и наметкой поверхность металла грунтуется меловой краской на клею.
При разметке однотипных деталей для массового и серийного производства пользуются металлическими или фанерными шаблонами. Разметка при помощи шаблонов называется наметкой. Инструментами для выполнения разметки и наметки служат чертилка из закаленной стали, кернеры, стальные линейки и угольники, стальные циркули и рейсмусы, молотки, клямеры, струбцины, стальные рулетки и др.
Резка. Резка металла на заготовки производится механическим способом на ножницах и пилах или газокислородным пламенем. Механическая резка производится в основном на ножницах и применяется преимущественно для прямолинейного реза листов толщиной до 20 мм. Наибольшее применение имеют гильотинные ножницы с ножами длиной от 1 до 3 м и пресс-ножницы с длиной ножей до 700 мм.
Для криволинейного реза толщин до 6 мм применяются роликовые ножницы с дисковыми ножами. Для прямолинейного реза больших толщин и дла криволинейного реза толщин свыше 6 мм применяется преимущественно газокислородная резка ручная, полуавтоматическая и автоматическая. Для холодной резки стержней круглого и других сечений применяются круглые (циркульные) зубчатые и фрикционные пилы.
Обработка кромок под сварку. Обработка и скос кромок под сварку производятся механическим путем на кромкострогальных и продольно-строгальных станках или газокислородным пламенем. При небольшом объеме работ иногда применяют рубку пневматическим зубилом. Гибка. Гибка листового, полосового и широкополосового металла производится на листогибочных трехвалковых и четырехвалковых вальцах. На холодную гибку поступают листы с подготовленными кромками и вырезанными отверстиями малых диаметров. Гибка профильного металла производится на правильно-гибочных прессах и роликовых гибочных станах. Наименьший допустимый радиус гибки стали в холодном состоянии рекомендуют брать равным 25-кратной толщине листа или высоте симметричного профиля. Если радиус холодной гибки меньше 25 толщин деформируемой стали, то возможны надрывы наружных волокон.
Гибка больших толщин и гибка обечаек малого диаметра, при средней толщине листа, производится горячим способом в кузнечно-прессовых цехах. Нагрев деталей производится до температуры 1000--1100°С, при которой металл легко поддается деформированию. Подготовку кромок под сварку и вырезку больших отверстий производят после горячей гибки.
Разделка кромок - придание кромкам, подлежащим сварке, необходимой формы.
Разделка кромок под сварку выполняется с целью обеспечения:
Провара по всей толщине свариваемых элементов;
Доступа сварочного инструмента к корню шва.
По форме разделки кромок под сварку различают сварные соединения без разделки кромок, с отбортовкой и с разделкой кромок под сварку. Кроме того, сварные соединения с разделкой кромок подразделяются на сварные соединения с односторонним скосом одной или двух кромок (односторонняя разделка одной или двух кромок) и сварные соединения с двусторонним скосом одной или двух кромок (двусторонняя разделка одной или двух кромок).
При выборе формы разделки кромки следует учитывать, что наиболее экономичным является сварное соединение без скоса кромок. В случае выполнения разделки кромок более простой в исполнении по сравнению с U- образной является разделка кромок с прямолинейным скосом кромок (V, К, Х - образные). В сравнении с односторонней разделкой кромок более технологичными являются К- и Х-образные двусторонние. Однако К- и Х-образные двусторонние могут быть реализованы при возможности доступа сварочного инструмента к обеим сторонам изделия.