Технологічний процес ручного дугового зварювання. Підготовка кромок під зварювання
Найпростіше, що потрібно знати зварювальникові-початківцю, це те, як стикаються між собою зварні деталі. Залежно від проектного положення, за правилами ГОСТ та БНіП існують різні видизварних з'єднань, як показано на малюнку нижче. Це стосується не лише пластин, а й куточків, швелерів, труб, квадратів та інших прокатних виробів.
Жодне більш-менш серйозне будівельне виробництвоне обходиться без застосування низької та середньої потужності. У меншій кількості випадків (коли немає доступу до електрики) види зварних швів виконуються, яка менш поширена через її більшу громіздкість.
У будь-якому випадку мало знати і вміти користуватися зварювальним апаратом для того, щоб зварити ті чи інші деталі. Важливо знати, які бувають види зварного шва, тобто, як робити обробку кромок деталей для їх стикування, фіксації в тому чи іншому просторовому положенні та подальшого їх зварювання.
Як правило, той чи інший вид шва зварного з'єднання формується за допомогою електроінструменту – болгарка з двома типами кіл: відрізний по металі та кутовий шліфувальний. Перший призначений для обрізання деталі під тим чи іншим кутом, другий – для обробки, їх відрізних поверхонь, шліфування, щоб вони рівно прилягали одна до одної. Крім того, сам зварювальний апаратздатний працювати у режимі різання.
У разі обидві деталі з'єднуються торцями, які заздалегідь спеціальним чином обробляють, або залишають необробленими. Це залежить від товщини металу деталей, з'єднання яких передбачається виконати.
Також варто звернути увагу на те, що може бути оброблений торець тільки однієї деталі, що дозволяє зменшити витрату металу, зварювального дроту при солідній товщині деталей. Крім цього, види стикових з'єднаньможуть бути оброблені з одного боку – для одностороннього зварювання та з двох сторін – для двостороннього зварювання.
З'єднання без обробки не обробляється будь-яким чином, тільки можливо забираються зазубрини, нерівності та шорсткості, щоб зробити стикування з зазором не більше 2 мм, як належить за ГОСТ. Буває одностороннім та двостороннім, відповідно розраховано на зварні стикові з'єднання деталей, товщина металу яких не перевищує 4 мм та 8 мм відповідно.
З'єднання зі скосом торців виконується у багатьох варіаціях, як показано на рис. Це може бути і односторонній рівний/овальний скіс кромки, і двостороння обробка, так званий V-подібний U-подібний скіс. Застосовуються всі ці типи стикових з'єднань для деталей із товщиною металу 4-25 мм із зазором 1-2 мм.
З'єднання з двостороннім обробленням має сенс виконувати при товщині деталі, що зварюється від 12 мм, так як саме з цієї величини починаючи можна помітити зниження витрати матеріалу для зварювання, металу. При цьому і саме зварювання стикових з'єднань відбувається швидше, ніж у випадку з одностороннім обробленням кромок за V-подібним або U-подібним способом, а витрата зварювальних матеріалівзменшується вдвічі як мінімум.
Як можна помітити, деталі мають положення, що нагадує букву "Т", звідси іменується як таврове з'єднання, при якому одна деталь знаходиться перпендикулярно до другої. Таким чином, зварюванням з'єднується поверхню кромки однієї деталі з поверхнею площинної другий. Відповідно оброблятися обробкою може лише одна деталь, як на малюнку нижче.
З'єднання без обробки зварюється з двох сторін і застосовується для деталей однакової товщини металу, що не перевищує 10 мм. Жодної особливої обробки кромки перпендикулярно розташованої деталі не застосовується, лише шліфування при необхідності для щільного прилягання кромки до площини (до 2 мм зазор). Важливо врахувати, що зварювання таврових з'єднань без обробки відрізняється у разі, якщо перпендикулярно розташована (вертикально стоїть) деталь має меншу товщину, ніж друга, що горизонтально примикає. Просто електрод ставлять під кутом 60 градусів до товстішої деталі, що сприяє більшому її плавленню.
З'єднання з обробкою виконується у разі, якщо потрібно особливо міцний шов та таврове зварне з'єднаннямає перпендикулярно деталь, що розміщується (вертикально стоїть), товщина металу якої більше, ніж 10 мм (як мінімум – 8 мм). Це може бути і одностороннє і двостороннє оброблення, при цьому край обрізають прямолінійно, під кутом 45 градусів. Так, зварювання великої товщини деталей відбувається в кілька шарів, поки не заповниться все навколо обробного простору.
У випадку, коли виробляється з'єднання внахлест, одна деталь розташовується на інший, зварювання відбувається по краях обох деталей. При цьому обробка кромок не передбачається технологічно, лише підготовка для щільного прилягання однієї площини до другої. З'єднуються деталі двома зварними швами, які зв'язують кромки з площинними поверхнями, що ближче лежать.
З'єднання без посилення найдоцільніше проводити при з'єднанні внахлестку деталей, що мають товщину не більше 10 мм. Подвійний шов у цьому випадку виконують з міркувань герметизації, тобто для того, щоб волога не потрапляла між нахлестом і не відбувався посилений процес корозії. Сам спосіб з'єднання називається «з'єднання внахлестку з лобовими швами».
З'єднання з посиленням виконується при особливих вимогах до міцності, а також за великої товщини металу виробів, що зварюються. На малюнку показано зварне з'єднання внахлест з додатковими зварними кріпленнями, які отримують шляхом прогрівання нижньої та проплавлення верхньої деталі, а також ті, що заздалегідь пропилюють у місці зварного з'єднання. Крім допоміжних кріплень, в окремих випадках вони можуть також виконуватися без лобових швів при невеликій товщині виробів, але в такому випадку на особливу міцність не варто розраховувати.
Дане з'єднання частково схоже на таврове через перпендикулярно розміщені зварні деталі. Подібно до таврового, кутове з'єднання обробляється лише однією стороною кромки, друга також бере участь у зварному процесі, але обробці не піддається, лише рівному обрізанню строго під 90 градусів і шліфування від задирок, зазубрин і т. д., інших дефектів.
З'єднання без обробки кромки, як показано на рис, проводиться зі зміщенням деталі з-під заподлицо другої кромки. При цьому зварювальний шовз'єднує обидва торці з зовнішнього боку, але кутові зварні з'єднання можуть бути додатково посилені і другим швом, виконаним з внутрішньої стороникута. При цьому другий шов зварює внутрішні площини деталей, при цьому збільшується витрата матеріалу для зварювання та час зварювання, але виходить міцне зварне з'єднання.
З'єднання з обробкою кромки застосовуються у разі великої товщини деталей, як і при таврових з'єднаннях. Одностороння або двостороння обробка кромки потрібна у випадку, якщо зварювання кутових з'єднань деталей з товщиною від 8 мм до 25 мм. При односторонній обробці виходить дуже глибокий шов, у зв'язку з цим зварювання роблять у 2-3-4 шари. Двостороннє V-подібне зварювання значно економічніше і швидше у виробництві в багатьох випадках.
Це була стаття про підготовку та стикування зварних з'єднань під ручне зварювання– найменша крупинка у пізнанні процесів зварювального виробництва. Окремою темою є те, як види зварних з'єднань та швів, описаних раніше, зробити тим чи іншим типом зварювання.
Зміст книги Наступна сторінка>>
Підготовка кромок для зварювання. Форма підготовлених кромок під зварювання.
Підготовка кромок для зварювання.До елементів геометричної форми підготовки кромок під зварювання (рис. 25) відносяться кут обробки кромок α, притуплення кромок S, довжина скосу листа L за наявності різниці товщин металу, зміщення кромок щодо один одного б, зазор між кромками, що стикуються, а.
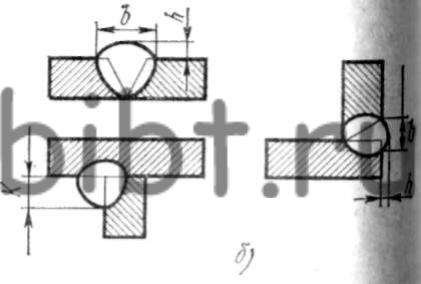
Рис. 25. Елементи геометричної форми підготовки кромок під зварювання (а)та шва (б):
в – ширина шва, h – висота шва, К – катет шва
Кут оброблення кромок виконується при товщині металу більше 3 мм, оскільки її відсутність (розробки кромок) може призвести до непровару по перерізу зварного з'єднання, а також до перегріву та перепалу металу; за відсутності обробки кромок для забезпечення провару електрозварювальник повинен збільшувати величину зварювального струму.
Обробка кромок дозволяє вести зварювання окремими шарами невеликого перерізу, що покращує структуру зварного з'єднання та зменшує виникнення зварювальних напружень та деформацій.
Зазор, правильно встановлений перед зварюванням, дозволяє забезпечити повний провар перерізу з'єднання при накладенні першого (кореневого) шару шва, якщо підібраний відповідний режим зварювання.
Довжиною скосу листа регулюється плавний перехід від товстої деталі, що зварюється до більш тонкої, усуваються концентратори напруг у зварних конструкціях.
Притуплення кромок виконується задля забезпечення стійкого ведення процесу зварювання під час виконання кореневого шару шва. Відсутність притуплення сприяє утворенню пропалів при зварюванні.
Зміщення кромок створює додаткові зварювальні деформації та напруги, тим самим погіршуючи властивості міцності зварного з'єднання. Зміщення кромок регламентується або ГОСТами, або технічними умовами. Крім того, зміщення кромок не дозволяє отримувати монолітного зварного шва по перерізу кромок, що зварюються.
ГОСТ 5264-80 передбачає для стикових з'єднань форми підготовлених кромок, що представлені на рис. 26; для кутових з'єднань – на рис. 27; таврових – на рис. 28 та нахлесткових - на рис. 29.
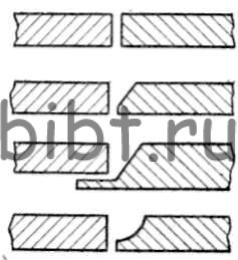
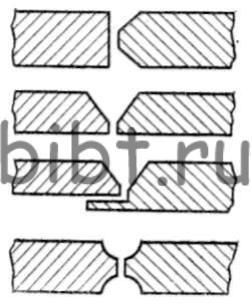
Рис. 26. Форма підготовлених кромок під зварювання для стикових з'єднань
Рис. 27. Форма підготовлених кромок під зварювання для кутових з'єднань

Рис. 28. Форма підготовлених кромок для зварювання для таврових з'єднань.
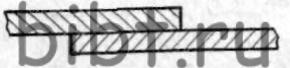
Рис. 29. Форма підготовлених кромок під зварювання для нахлесткових з'єднань
Підготовку кромок під зварювання виконують на механічних верстатах -токарних (обробка торців труб), фрезерних, стругальних - обробка листів і т. д., а також застосуванням термічного різання. Листи, труби, виготовлені з вуглецевих сталей, обробляються газокисневою різкою. Як горючі гази можуть служити ацетилен, пропан, коксовий газ і т. д. Кольорові метали, а також нержавіючі сталі обробляються плазмовою різкою.
Перед зварюванням особливо відповідальних конструкцій торці труб або листів після газокисневого різання обробляють додатково механічним шляхом; це робиться для того, щоб уникнути будь-яких включень у металі.
РОЗДІЛ КРОМОК ПІД ЗВАРЮВАННЯ
Обробка країв - надання крайкам, що підлягають зварюванню, необхідної форми.
Обробка кромок під зварювання виконується з метою забезпечення:
Провара по всій товщині елементів, що зварюються;
Доступу зварювального інструменту до кореня шва.
За формою оброблення кромок під зварювання розрізняють зварні з'єднання без оброблення кромок, з отбортовкой і обробкою кромок під зварювання. Крім того, зварні з'єднання з обробкою кромок поділяються на зварні з'єднання з одностороннім скосом однієї або двох кромок (одностороння обробка однієї або двох кромок) і зварні з'єднання з двостороннім скосом однієї або двох кромок (двостороннє оброблення однієї або двох кромок).
При виборі форми оброблення кромки слід враховувати, що найбільш економічним є зварне з'єднання без скосу кромок. У разі виконання оброблення кромок простіший у виконанні порівняно з U – подібним є обробка кромок з прямолінійним скосом кромок (V, К, Х – образні). У порівнянні з одностороннім обробленням крайок більш технологічними є К- і Х-подібні двосторонні. Однак К- та Х-подібні двосторонні можуть бути реалізовані за можливості доступу зварювального інструменту до обох сторін виробу.
Конструктивні елементи форми обробки кромок.
Конструктивні елементи форми оброблення кромок залежать від конструктивних особливостей елементів, що зварюються, а також від діаметра електродного матеріалу (розміри оброблення кромок повинні забезпечувати доступ електрода або зварювального дроту до кореня шва).
Форма обробки кромок характеризуються такими основними конструктивними елементами: зазор b, притуплення С, кут скосу кромки і кут обробки кромок.
Кут скосу краю β.
Скос кромки - прямолінійний зріз кромки, що підлягає зварюванню.
Кут скосу кромки – гострий кут між площиною скосу кромки та площиною торця.
Кут скосу кромки β змінюється в межах від 30±5 до 10±5 градусів. При обробці однієї кромки кут скосу краю може становити 45 градусів.
Кут оброблення кромок- Кут між скошеними кромками частин, що зварюються. Кут обробки кромок α= 2 β. Кут оброблення кромок виконується для забезпечення доступу електрода до основи шва.
Притуплення краю- Нескошена частина торця кромки, що підлягає зварюванню. Призначення притуплення - забезпечити правильне формування зварного шва та запобігти пропаленням у корені шва. Притуплення країв Ззазвичай становить 2 мм ± 1 мм. Іноді, у зв'язку з конструктивними особливостями зварного з'єднання значення притуплення може прийматися рівним нулю (С=0). У цьому випадку необхідно передбачати технологічні заходи, що виключають появу пропалу (зварювання на підкладці, зварювання на флюсовій подушці, укладання підварювального шва, застосування замкового з'єднання).
Проміжок- найкоротша відстань між кромками зібраних для зварювання деталей. Зазор bзазвичай дорівнює 1,0 - 3 мм, так як при прийнятих кутах обробки крайок наявність зазору необхідна для провару кореня шва, але в окремих випадках, при тій чи іншій технології, зазор може дорівнювати нулю або досягати 8-10 мм і більше. Якщо зазор b = 0, зварювання називається зварюванням без зазору, якщо b ≠ 0 –зварюванням із зазором (або за зазором).
БЕЗ РОЗДІЛКИ КРОМОК |
§ 28. Підготовка металу під зварювання
Підготовка металу під зварювання.При підготовці деталей під зварювання метал, що надходить, піддається правці, розмітці, намітці, різанні, підготовці кромок під зварювання, холодній або гарячій згинанні.
Метал правлять або вручну або на різних листоправильних вальцях. Ручне виправлення виконують на чавунних або сталевих правильних плитах ударами кувалди або за допомогою гвинтового ручного преса. Кутова сталь правиться на правильних вальцях (пресах), двотаври та швелери - на приводних або ручних правильних пресах.
Розмітка та намітка – це такі операції, які визначають конфігурацію майбутньої деталі. Механічна різка застосовується для прямолінійного різання листів, а іноді для криволінійного різання листів з використанням для цієї мети роликових ножиць з дисковими ножами. Вуглецеві сталі розрізають газокисневою та плазмово-дуговою різкою. Ці способи можуть бути ручними та механізованими. Для різання легованих сталей, кольорових металів може застосовуватися газофлюсове або плазмово-дугове різання.
Основний метал і присадковий матеріал перед зварюванням повинні бути ретельно очищені від іржі, олії, вологи, окалини та різного роду неметалевих забруднень. Наявність зазначених забруднень призводить до утворення в зварних швахпір, тріщин, шлакових включень, що призводить до зниження міцності та щільності зварного з'єднання.
Підготовка кромок для зварювання.До елементів геометричної форми підготовки кромок під зварювання (рис. 25) відносяться кут обробки кромок α, притуплення кромок S, довжина скосу листа L за наявності різниці товщин металу, зміщення кромок щодо один одного б, зазор між кромками, що стикуються, а.
Рис. 25. Елементи геометричної форми підготовки кромок під зварювання (а) та шва (б):
в – ширина шва, h – висота шва, К – катет шва
Кут оброблення кромок виконується при товщині металу більше 3 мм, оскільки ця відсутність (розробки кромок) може призвести до непровару по перерізу зварного з'єднання, а також до перегріву та перепалу металу; за відсутності обробки кромок для забезпечення провару електрозварювальник повинен збільшувати величину зварювального струму.
Обробка кромок дозволяє вести зварювання окремими шарами невеликого перерізу, що покращує структуру зварного з'єднання та зменшує виникнення зварювальних напружень та деформацій.
Зазор, правильно встановлений перед зварюванням, дозволяє забезпечити повний провар перерізу з'єднання при накладенні першого (кореневого) шару шва, якщо підібраний відповідний режим зварювання.
Довжиною скосу листа регулюється плавний перехід від товстої деталі, що зварюється до більш тонкої, усуваються концентратори напруг у зварних конструкціях.
Притуплення кромок виконується задля забезпечення стійкого ведення процесу зварювання під час виконання кореневого шару шва. Відсутність притуплення сприяє утворенню пропалів при зварюванні.
Зміщення кромок створює додаткові зварювальні деформації та напруги, тим самим погіршуючи властивості міцності зварного з'єднання. Усунення кромок регламентується або ГОСТами, або технічними умовами. Крім того, зміщення кромок не дозволяє отримувати монолітного зварного шва по перерізу кромок, що зварюються.
ГОСТ 5264-80 передбачає для стикових з'єднань форми підготовлених кромок, що представлені на рис. 26; для кутових з'єднань – на рис. 27; таврових – на рис. 28 та нахлесткових - на рис. 29.
Рис. 26. Форма підготовлених кромок під зварювання для стикових з'єднань
Рис. 27. Форма підготовлених кромок під зварювання для кутових з'єднань
Рис. 28. Форма підготовлених кромок під зварювання для таврових з'єднань
Рис. 29. Форма підготовлених кромок під зварювання для нахлесткових з'єднань
Підготовку кромок під зварювання виконують на механічних верстатах - токарних (обробка торців труб), фрезерних, стругальних - обробка листів тощо, а також застосуванням термічного різання. Листи, труби, виготовлені з вуглецевих сталей, обробляються газокисневою різкою. Як горючі гази можуть служити ацетилен, пропан, коксовий газ і т. д. Кольорові метали, а також нержавіючі сталі обробляються плазмовою різкою.
Перед зварюванням особливо відповідальних конструкцій торці труб або листів після газокисневого різання обробляють додатково механічним шляхом; це робиться для того, щоб уникнути будь-яких включень у металі.
Вимоги до збирання металевих деталейперед зварюванням.Складально-зварювальні пристрої, що застосовуються, повинні забезпечувати доступність до місць встановлення деталей і прихваток, до рукояток фіксуючих і затискних пристроїв, а також до місць зварювання. Ці пристрої повинні бути досить міцними і жорсткими, забезпечувати точне закріплення деталей в потрібному положенні і перешкоджати їх деформуванню в процесі зварювання. Крім того, складально-зварювальні пристрої повинні забезпечувати найвигідніший порядок збирання та зварювання: найменше числоповоротів при накладенні прихваток та зварних швів; вільний доступ для перевірки розмірів виробів та їх легке знімання після виготовлення; безпека складально-зварювальних робіт.
Будь-яка складальна операція не повинна ускладнювати виконання наступної операції. Деталі, що надходять на складання, повинні бути ретельно перевірені; перевірці підлягають всі геометричні розміри деталі та підготовлена форма кромок під зварювання.
Складання зварних конструкцій, як правило, здійснюється або за розміткою, або за допомогою шаблонів, упорів, фіксаторів або спеціальних пристроїв - кондукторів, що полегшують складальні операції. Підготовку та складання виробів під зварювання виконують з дотриманням наступних основних обов'язкових правил:
притуплення кромок та зазори між ними повинні бути рівномірними по всій довжині;
кромки елементів, що підлягають зварюванню, та прилеглі до них місця шириною 25-30 мм від торця кромки повинні бути висушені, очищені від грата після різання, олії, іржі та інших забруднень;
щоб уникнути деформацій, прихватку слід виконувати якісними електродами через інтервал не більше 500 мм при довжині однієї прихватки 50-80 мм;
для забезпечення нормального та якісного формування шва потрібно на початку та в кінці виробу прихоплювати планки.
У підготовку металу під зварювання входить правка, розмітка та намітка, різання та обробка кромок, холодна та гаряча згинання. Виправлення здійснюється переважно на верстатах, а іноді вручну. Листовий, смуговий та профільний прокат правлять на вальцях, які найчастіше мають сім чи дев'ять валків.
Вальці обладнуються двома роликовими столами для завантаження та виходу металу в процесі редагування. При правці листи пропускають через вальці від 3 до 5 разів.
Поряд із машинною правкою іноді застосовують ручну правку. Останню виробляють на чавунних чи сталевих правильних плитах ударами молота, кувалди та за допомогою гвинтового пресу.
Виправлення кутової сталі роблять на кутоправильних вальцях або на ручних гвинтових пресах, а двотаврів і швелерів - на приводних або ручних правильних пресах.
Розмітка та намітка. При індивідуальному виробництві виправлений метал надходить на розмітку, а при масовому та серійному виробництві надходить для намітки. Перед розміткою та наміткою поверхня металу ґрунтується крейдовою фарбою на клеї.
При розмітці однотипних деталей для масового та серійного виробництва користуються металевими чи фанерними шаблонами. Розмітка за допомогою шаблонів називається наміткою. Інструментами для виконання розмітки та намітки служать креслила із загартованої сталі, кернери, сталеві лінійки та косинці, сталеві циркулі та рейсмуси, молотки, клямери, струбцини, сталеві рулетки та ін.
Різання. Різання металу на заготовки проводиться механічним способом на ножицях та пилках або газокисневим полум'ям. Механічна різка проводиться в основному на ножицях і застосовується переважно для прямолінійного різання листів завтовшки до 20 мм. Найбільше застосування мають гільйотинні ножиці з ножами довжиною від 1 до 3 м та прес-ножиці з довжиною ножів до 700 мм.
Для криволінійного різу товщин до 6 мм застосовуються роликові ножиці з дисковими ножами. Для прямолінійного різання великих товщин і для криволінійного різання товщин понад 6 мм застосовується переважно газокисневе різання ручне, напівавтоматичне та автоматичне. Для холодного різання стрижнів круглого та інших перерізів застосовуються круглі (циркульні) зубчасті та фрикційні пилки.
Обробка країв під зварювання. Обробка та скіс кромок під зварювання виробляються механічним шляхом на кромкостругальних та поздовжньо-стругальних верстатах або газокисневим полум'ям. При невеликому обсязі робіт іноді застосовують рубку пневматичним зубилом. Гнучка. Гнучка листового, смугового та широкосмугового металу проводиться на листозгинальних тривалкових та чотиривалкових вальцях. На холодну згинання надходять листи з підготовленими кромками та вирізаними отворами малих діаметрів. Гнучка профільного металу проводиться на правильно-згинальних пресах та роликових згинальних станах. Найменший допустимий радіус згинання сталі в холодному стані рекомендують брати рівним 25-кратній товщині листа або висоті симетричного профілю. Якщо радіус холодної згинання менше 25 товщин деформованої сталі, то можливі надриви зовнішніх волокон.
Гнучка великих товщин і згинання обічайок малого діаметра, при середній товщині листа, проводиться гарячим способом у ковальсько-пресових цехах. Нагрів деталей проводиться до температури 1000-1100°С, при якій метал легко піддається деформуванню. Підготовку кромок під зварювання та вирізування великих отворів проводять після гарячої згинання.
Обробка кромок - надання кромок, що підлягають зварюванню, необхідної форми.
Обробка кромок під зварювання виконується з метою забезпечення:
Провара по всій товщині елементів, що зварюються;
Доступу зварювального інструменту до кореня шва.
За формою оброблення кромок під зварювання розрізняють зварні з'єднання без оброблення кромок, з отбортовкой і обробкою кромок під зварювання. Крім того, зварні з'єднання з обробкою кромок поділяються на зварні з'єднання з одностороннім скосом однієї або двох кромок (одностороння обробка однієї або двох кромок) і зварні з'єднання з двостороннім скосом однієї або двох кромок (двостороннє оброблення однієї або двох кромок).
При виборі форми оброблення кромки слід враховувати, що найбільш економічним є зварне з'єднання без скосу кромок. У разі виконання оброблення кромок простіший у виконанні порівняно з U-подібною є обробка кромок з прямолінійним скосом кромок (V, К, Х - образні). У порівнянні з одностороннім обробленням крайок більш технологічними є К- і Х-подібні двосторонні. Однак К- та Х-подібні двосторонні можуть бути реалізовані за можливості доступу зварювального інструменту до обох сторін виробу.